Brotherhood Of Steel Armor Fallout 3
In this tutorial, I will show you how to create a helmet based on the Brotherhood of Steel from Fallout 3.The finished helmet is comprised of a main body and a series of numerous attached accessories.This guide will take you through the process of:.Planning.Helmet Modeling.Helmet Molding.Helmet Casting.Accessories.Painting.Assembly.Recycling your siliconePlease note that the Materials and Tools listed at the beginning of each chapter will only pertain to that particular phase of the project. Keep this in mind as you budget your expenses since this can become very expensive if you buy too much at once.
NOTE- you can skip this step if you do not have 3D experience or do not wish to modify the design.The Pepakura file that I've built is available here (simply remove the 'dot' from the address below):paper model that I built was derived from the 3D model in the game. You can build your own from scratch or use the model from the game as a guide. The PC edition of Fallout 3 includes the G.E.C.K. (Garden of Eden Creation Kit) which gives you access to the different model assets used in the game.
To extract the helmet you are going to need to download a free program called Nifskope. Fallout features a massive library of assets.
The model you will want can be found under: meshesarmorpowerarmorhelmet.nifExport this helmet mesh as an.obj. We will need to edit the mesh in another 3D package before we can make the paper model. NOTE- you can skip this step if you do not have 3D experience or do not wish to modify the design.The Pepakura file that I've built is available here (simply remove the 'dot' from the address below):the.obj of the helmet into your 3D package. First we will need first to remove all of the details (hoses, lamps, scopes, etc) until nothing remains but the main body of the helmet. All of those other details will be built, but with different methods.Once this is done we will need to rebuild the mesh to remove as many triangular polygons (or 'tris') as possible. Triangular polygons are fine for a low-resolution, in-game asset, but the paper model we'll make needs clean quadrangular polygons ( or 'quads').
Clean loops and strips of Quads will unfold into flat paper shapes better than the Tris and just look better too. It will really help your model stand out from hobbyists who are making papercraft models from raw in-game models. Unfortunately, what looks good animating in a game doesn't always translate to a static sculpture that you can closely examine, so it's best to refine it and add a little more definition.Export your quaded model as a new.obj. NOTE- the Pepakura file that I've built is available here (simply remove the 'dot' from the address):Pepakura Designer and import the quaded helmet.obj. You will need Pepakura to arrange the polygons into sheets of paper that you can later print out, cut up, and assemble into a model. This works best when you arrange the polys into groups of strips.
As you can see in the picture, Pepakura will arrange these groups onto as many sheets of paper as you need to complete the model. In this case, there were enough polygons to fill 12 sheets of 8.5x11.Paper however is not ideal for your model since it is too flimsy. I would recommend printing onto card stock, which is sturdier. If you don't have a printer that can handle card stock (or you just don't have any) you can print this on regular paper and then have them copied onto card stock at any print shop for only a few cents apiece.I used Kinkos (?).Fed Ex/Kinkos (?).Fed-Ex Office (?).or whatever it's called now.Printy McPrintertons? While the Pepakura method of sculpting can be very exact it can also result in models that appear too 'low poly'. I've found that applying layers of cheese cloth will smooth out the polygonal look and add some non-rigid surface strength. The practice is not unlike laying-up fiber glass (although far less toxic and can be done indoors).
Cut strips of cheesecloth, lay them against the surface of the model, and brush the acrylic gel into the weave of the cloth. You'll want to to dilute the gel with just a little bit of water to allow the gel to better saturate the weave. Too much water will soak and warp the underlying card stock (thus defeating the purpose of reinforcing the surface). Continue this process by overlapping pieces of cloth until you've covered the sculpt.Another nice side effect of this technique is that it unifies any underlying details you may have added with an acrylic 'skin' of cloth.
Now that the helmet has been skinned with cheese cloth, it's time to begin refining and smoothing the surface. For this we will use the DAP DryDex spackle. It can be used safely indoors (unlike Bondo) and sands to a glassy finish.
Use a pallet knife to apply the DryDex and steel scraper clay tool to blend it in. The compound goes on pink but turns white as it dries.
Once it everything is dry you can begin sanding down. Start with coarse paper (120 grit) to get rid of the sharper bits and continue to refine the surface with 240 and 320 grit paper. You can take it a step further with 600 grit paper to get to that glassy finish.I built some extra details like the rear hose attachment and the rim base from foam core and card stock.
I also refined the respirator hose attachments and ear setting in 3D and prepared them in Pepakura. All of these extra details are blended into the rest of the helmet with DryDex and sanded smooth.The file for the ear setting and hose attachments are available here if you don't want to sculpt the refinements:http://www.4shared.dot.com/file/YdQ-isco/NozzlesPep.html. At this point we're going to add some accents to the brows and center ridge. I used red electrical wire (as pictured) for my helmet but the better option is half-round styrene rods. Styrene is more flexible, easier to cut, and easier to affix with super glue. Use the.125 half-round rods where you see the red wire used in my example.Cutting styrene can be rather easy because it isn't always necessary to cut all the way through.
The plastic has no grain, so you can cut or score the surface and then bend it until it snaps clean. We now begin the Base model that will serve as the foundation for the mouth respirator and ear knobs.
Cut a circle of foam core with a 3 inch diameter. Draw a 2 inch circle at the center to indicate the space we need to leave open. Cut a 2 inch circle of foam core and glue it into that center area. The middle area needs to open in the final shape but we need a starting point for wrapping the strips of styrene.Cut numerous strips of styrene at varying widths (wide to narrow).These strips should be long enough to be wrapped around your shape.Start by laminating the widest strips to the 2 inch piece of foam core at the center. Work your way to the perimeter by wrapping and laminating narrower strips until you reach the edge of the part. This should result in a sloping profile shape.
Once that's finished, apply Squadron modelling putty to smooth the edges between the strips. This will create a nice tapering profile. After the putty is dry, sand away the excess taking care to use even motions all the way around the shape. Consistency is crucial for maintaining roundness. Too much putty or too much sanding in one spot can result in a lopsided shape.
We're going to take a bit of a break from the modeling to touch on some simple mold making. We need to make some copies of the Base to which we will affix the the mouth respirator and ear knobs. Luckily, this first mold is a 1-part mold, which is pretty easy. We won't be concerning ourselves with parting lines, pouring holes, or air holes.We begin by fixing the part you just made to a flat, clean surface with some Klean Klay and building some walls around it from foam core. What we're doing is building a container around the part so we can pour in the silicone rubber. Take care to glue everything so there are no cracks in your container.
We don't want the liquid rubber to leak. Silicone rubber can be expensive, so you don't want to waste it on a shoddy, leaky mold.I prefer using Legos to build my mold walls (as you can see in the picture). The blocks interlock tightly, do not leak, and are easier to assemble than cutting and gluing the walls and base from foam core.The silicone rubber is a 2-part mixture that consists of liquid rubber and catalyst (or hardener). There should be directions on the package for how to mix them but the ratio is typically 10 to 1. That is, to catalyze 100 ml of liquid rubber you will need to use 10 ml of catalyst. Pour the liquid silicone into a measured mixing cup like the one in the picture. Then pour in the proper amount of catalyst.
Using a craft stick, mix the rubber and catalyst slowly and thoroughly to make sure there are no air bubbles. The rubber takes about 8 hours to completely set so take your time. Once you are ready you can pour it into your mold. Do not pour the rubber directly onto your part. Pour it around the deepest part of mold and allow it to rise around your part until it fills the container.
Pour it slowly in an even stream to prevent any air bubbles from forming. Air bubbles can result in flawed casts that need to be filled or sanded. Once the mold is filled you can tap the side of it to shake free any bubbles that might be clinging to the part. They should float to the surface and dissipate.Once this is all done you will need to leave the mold to set. Put it some place where it will not be bumped while it cures otherwise your mold will warp and create distorted casts.Let the mold set for 8 hours. I like to prepare my molds in the morning before I leave for work, that way there is no temptation on my part to hover over it and poke at it (I'm impatient like that). Do not throw away the cured silicone of a bad mold.
You can recycle it, which we will discuss later. Once the mold has fully cured, you can begin the process of demolding your part (separating the mold from the original piece) and preparing for casting. Dismantle the walls around your mold until the cured silicone is fully exposed and then (gently) begin peeling away the mold from the base. Take care while doing this so you do not tear and thin parts of rubber and ruin a perfectly good mold.Now that your mold is free, you can prepare it for casting your 3 copies. Spray the mold (in a well ventilated area) with the Ease Release spray and let it set for a few minutes.
The Release spray prevents the casts from when you demold them and will extend the life of your mold.The casting resin is a 2-part mixture with a 1:1 ratio consisting of Part A and Part B chemicals. That is, if you need to use 50 ml of resin to fill a mold, you would use 25 ml of Part A and 25 ml of Part B.
Nice and Easy. Pour even amounts of Parts A and B into their own measuring cups. You'll notice that each chemical is clear and colored.
They will become an opaque white (or off-white) after they are mixed, begin to catalyze, and harden. Unlike the silicone rubber, most casting resins will harden in minutes rather than hours. There are casting resins that take hours to harden (like Feather Lite), but we're not using them here.Once you are ready, you can then pour them together into a third mixing cup. Stir the mixture slowly to remove any air bubbles but be aware that (once mixed) the resin is already beginning to catalyze and harden. Do not stir too quickly because it will only hasten the cured. You may feel some warmth in the mixing while stirring the mixture.
This is due to the chemical reaction of mixture. Large enough mixtures can get very hot so be careful not to spill any of it on yourself.Slowly pour the mixture into the mold. Again, you'll want to try to pour mix into the deepest part of the mold and let it fill. Do not pour it on the wall of the mold where it will run 'downhill' before filling. Once the mold is filled you can watch in real time as the clear mixture will become frosty and opaque.
You'll feel the heat from the reaction if you hold your palm over the mold (do not touch it). The mixture will cool as the chemicals complete the reaction completes. Your part should be ready for demolding in about 10 minutes.
Again, take care in removing the cast so you don't tear the mold. Also, I suggest leaving your parts in the mold until they are cool to the touch.Repeat this 2 more times until you have your 3 Base casts. Once you have the 3 pieces it's a good idea to rinse them off with warm, soapy water. This will remove the oily film of the Ease Release and make it easier to glue to the helmet and later prime.Once your parts are rinsed and dried you can then glue them to the flat areas of the mouth and ears. The next part that we need to mold and cast are the ear pieces. You can see in the highlighted area of the photo how the cast of the ear piece fits into the base part(s) we just made. This part will be easy to model since we will be making a mold of a found-item rather than scratch building one.
I found that the top of an old spray can is the perfect size and shape for the ear. It's not safe to go sawing into a pressurized spray can, so we're just going to use silicone rubber to make a mold of one instead and copy the casts to each side of the head.Find an old spray can that you don't need, remove the nib, and plug it with some Klean Klay. We'll want to build a foam core container around the top the spray can to hold in the silicone.
We'll begin by making the 'floor' of the mold container. It needs a hole in the center of it to allow the spray can to poke through the floor. Set the spray can on a piece of foam core and trace around the base of the can with a pen to find your circumference. Cut this circle away with an Xacto knife. Then glue the walls of the container to the four edges of the floor.
What you should have now is a container with a hole in the floor big enough to slide over the spray can. Slide this container over the can (as pictured in the Photoshop mock up) and seal the gaps with Klean Klay to prevent leakage.
Add clay to the underside of the container to support the weight of the mold.As instructed previously, mix a batch of silicone rubber, pour it in, and allow it to set for 8 hours.After 8 hours have passed you can remove the mold from the spray can. Treat the mold with a quick spritz of Ease Release. Mix a small batch of resin (you shouldn't need much) and fill the mold. Repeat this twice and you will have both ear parts. The ear piece protrudes quite a bit so you will need to use a hobby saw to remove about half an inch from the tops of each cast. Sand away any burs and nest them with super glue into the Base casts that you've attached to each ear area. This step covers the building of the respirator on the 'mouth' of the mask.
This part was challenging and I went through two iterations before I got it right but it still managed to be one of my favorite parts to make. Pure scratch building fun.The respirator will be built onto the remaining Base casting.
As you'll recall, we used the other two Bases as foundations for the ear parts. We're going to be using a sheets of the.040 styrene to make the respirator.
To make it fit we'll need to trace the upper part of the Base part onto the sheet of styrene. Flip the Base face down onto the sheet and trace the circumference with a pen. You should have a circular shape that fits the inset top of the Base.
When it finds the duplicate files you are able to select that which files to delete or to move. With the help of this program, you can easily and deeply scan all type’s files like photos, music, films, video, word documents, PowerPoint presentation and text files.When you are using the Duplicate Cleaner Pro then you have to just write the name of the file if it appears twice then this program will find it. You also have the option to delete it permanently or to delete to the recycle bin. Clave de licencia para duplicate cleaner 4.
Then we'll draw a radial design of 6 elongated air holes inside of that circle. Take your time and try to make them as even as possible to retain that mechanical look.
Cut out the circle and cut out the air holes. Trace the design of this piece onto your remaining styrene sheets and then cut it out so you have two identical parts. Laminate the two cut-outs onto your Base. Stacking them will create some depth in the air holes to nest the last details.Take some half-round styrene rods and wrap them around the circumference to hide any gap between respirator cut-outs and the Base cast. Use the alligator clamps to keep them in place while the super glue sets.The last step of this portion will be to add small open nozzles.
Use your hobby saw to cut short portions of tube (about 1/8 of an inch) like you see in the picture. Set these short segments of tube into the open air holes of the respirator with just a dab of super glue apiece. The modeling phase of the helmet is close to finished (treat yourself to something nice if you made it this far).
There are only a few more details to go before the helmet is ready for molding and casting.First off, we need to add the bolts that give the helmet that heavy, riveted look. Craft stores like AC Moore and Michaels carry buttons of fake pearls in their jewelry and scrap-booking sections that make very convincing bolts (see the pictures). While these buttons have sticky backs, you'll still need to use some super glue and putty to affix and blend them. The photos feature high lighted spots on the helmet where the button-bolts will need to go. You'll no doubt notice that the helmet has been painted black. When I made this particular helmet, I had forgotten to add the buttons until after the priming stage when I should have done them at this stage.You'll need to add two details that are not decorative. The first is a 1 inch circular shape beneath the left eye (left if you're looking out) and the second is a ring snap button on the 'cheek bone' just beneath the right eye.
You can build the first shape with foam core or kit bash it from a wheel in a model kit (I used a wheel from a mobile Scud launcher). It doesn't really matter if it's detailed since it's really only going to serve as a mounting surface for an accessory that we'll build later.You can buy ring snap buttons from just about any clothing or craft store. This is another important detail that we will be using as an attachment point for a future accessory.Until this point, the eyes had been left open to the interior of the helmet. We'll need to close them so we can make absolutely sure that the final cast will have an even surface that can accommodate the interior visor. Simply cut a piece of card stock and apply it to the interior of the helmet where your eyes would be.
Seal any gaps between the visor and helmet with spackle or putty.Now we'll finish any surface refinements before we seal it up and prime it for molding. Use the spackle or putty to fill any inconsistencies and imperfections on the rest of the helmet. I also added some strips of styrene the center ridges of the helmet to make them more mechanically even.Spot fill and sand down any trouble spots until you feel comfortable that you got it all. There's really no right or wrong level of polish at this stage. It's entirely up to you.
The mold we make will require that the helmet be completely sealed on all sides and that it features a pouring hole for the resin.Until now, the bottom of the helmet had been left open for portability but now we must seal it up. You'll need to first situate a 1 inch dowel in the very center of the helmet. This will not only serve as a stand of the helmet once it's right side up but will also serve as the pour hole for your resin. You'll need to get this in position before you fill it and seal it because the filler and sealer will hold it in place.Now we're going to fill it and seal it off.You can do this two different ways. You can fill the helmet with tightly crumpled newspaper or use something more rigid like liquid foam. I used (and suggest) the. It's a very simple 1:1 mixture that expands and cures extremely fast.
The cured foam can then be cut with a saw until it's a little even. If you do decide to use the liquid foam then be aware that it expands as it cures and requires very little to fill a space. It's very tenacious and likes to stick to things so you don't want to overdo it and allow it to overflow onto the exterior of the helmet. After the excess foam has been cut away, use the DryDex spackle to fill in any air bubble cavities and sand it down.The helmet needs to be able to rest in an upright position. Cut a wide wood plank (exact measures are not important) into 3 even lengths and sandwich them together. Then drill a hole with a 1 inch hole saw into the center of the plank. This should accommodate the dowel and provide a stable base for the helmet.
It helps to prime the surface of your model before you make a mold of it. Scratch built models (and especially kit bashed models) are often made from many different materials with varying surface qualities which can make it tough to identify surface blemishes.Spray your model with a coat of glossy black. This unifies the surface appearance and the gloss reveals the remaining irregularities and imperfections. Let the paint dry for at least a day before you begin to putty and sand the blemishes.
Give your model another coat once you are satisfied to double check your repairs. Repeat this process until you are satisfied.This process may sound laborious but it was recommended by fabricators who build custom car bodies.It's how they get all those custom panels so darn smooth. Tools and Materials.chip brushes.measured mixing cups.paint stirrers.Ease Release spray.Dremel w/ cutting wheel and drill bits.sand paper.screws w/ matching wing nuts.protective eye wear.vinyl gloves.OPTIONAL.-We now begin the process of making the mold from which you pull a light-weight wearable cast.The shape of your model will determine the complexity of your mold. The simple shapes that we've made so far were easily replicated with simple, 1-part molds. A shape as complex as your helmet would be impossible to replicate with a single mold.
You could coat the entire helmet in a thick coat of silicone but then you'd never be able to remove the model without destroying the mold and you could never pull cast from it either. In this instance, it will require a 3-piece set that consists of a mold of the front, a mold of the back, and a mold of the bottom. The molds are intended to join where they can part most easily from the original model and subsequent casts. You can find many videos on Youtube that elaborate on the basics of mold making if you need more information. I am only going to focus on the specifics of molding this particular project.We begin by creating the parting wall that divides the front from the back and the bottom.
I determined that the ear-line and the 'lower jaw' were the best places to build a dividing wall of Klean Klay. This dividing wall prevents the silicone from leaking into the areas we want to keep free of rubber. You'll want to create 'key shapes' in your clay. These shapes will allow the different parts of your mold to register with one another and interlock. In this instance, I used a long, narrow strip of clay and some simple wood pegs I had lying around.Build up the sides of the dividing wall to keep the silicone from spilling over the edge of the dividing wall. Now you're ready to mix and apply the silicone. We begin this stage by mixing our first batch of Rebound 25 silicone, which I recommend because it is formulated to adhere to large vertical surfaces and can either be poured onto your model or applied with a brush.
The mixture ratio of Rebound is different (and easier) from the silicone we used to make the Base parts. Rebound 25 mixes at 1:1 (unlike the previous 10:1) much like the casting resin. The silicone will be applied in phases. We'll begin with an impression coat that insures that all of the detail is captured by the rubber. I recommend using a small amount of to insure that the rubber runs into every area of detail.
You'll want to make sure that your model is also airtight. The diluted silicone will be fluid enough to run into any cracks you make have on your model. The last thing you'll want is rubber curing inside of your model. Apply this with a disposable chip brush until the entire surface is covered.
Don't worry if the rubber is filmy and only semi-opaque, since we will reinforce and thicken the coat. Allow this to cure for a minimum of 8 hours without touching the rubber.Mix another batch of silicone and pour small portions into little cups or a painting tray. We'll use these for the registration keys that' allow the mold to interlock with the jacket mold (see the circled areas in the image).
Allow these to cure and apply the rest of your batch with a brush to cover your impression coat. Allow this to cure for 8 hours.Mix a third and last batch and have your registration keys ready. I highly recommend using a at this stage so your registration keys will stay in place and your final coat is reinforced. You want to make sure you have a uniform thickness across the surface of about half an inch so the mold doesn't tear.Once the silicone is cured and you've removed your retaining walls of clay you will notice that excess silicone almost always strays from the mold. Cut that silicone away and hang onto to it to recycle later.
thickened silicone may be difficult to mix so use a heavy paint stirring stick. Now that you've finished the silicone mold of the front, you'll need to make what is called a jacket mold (or mother mold). The jacket mold provides rigid support for the flexible silicone mold inside. This will prevent the mold from flopping around during the casting process (which creates warped or broken models).
The size and weight of the finished mold calls for a light weight solution that is still strong and rigid, so we're going to use fiberglass.First some safety things to get out of the way. READ THIS.Before we get started you should know that the fiberglass resin is highly toxic and should only be used in well ventilated areas. The fiberglass mat cloth is also unsafe to handle with unprotected skin. I use disposable vinyl gloves.
It is quite literally fibrous glass and can irritate the skin and damage the eyes and the lungs. Make sure you use a respirator and not a dust mask.
A simple dust mask is not adequate. You do not want fiberglass in your lungs, in your eyes, on your skin, or in your hair. I like to wear a ball cap and hoodie to keep it out of my hair and use goggles instead of safety glasses to keep it out of my eyes. I've had flakes of fiber float over the edge of my glasses while cutting cured fiberglass with a Dremel. Rinsing glass particles out of your eyes is NOTfun.Also, do not try using fiberglass resin in the cold, since low temperatures will impede curing.As a rule, I do not ever work with fiberglass in temperatures below 60 degrees. So.The nozzles shapes on the front of the helmet do not allow for a single part jacket mold.
The underlying silicone mold is flexible enough to be pulled around. The cured fiberglass is not. The fiberglass jacket would be mechanically locked around the nozzles and be unable to be pulled away from the back. What we will need to do instead is build the front jacket mold in two pieces that screw together.
To do this, you'll need to create a parting wall of clay down the center of the face (as pictured) with key shapes that allow the two shells to interlock.Begin cutting your fiberglass mat into a pile of 4x4 inch squares. Cut enough squares to cover your mold and allow for about an inch of overlap on each side. Once you have finished, you will need to mix the fiberglass resin that you will use to laminate the fiberglass mat. Fiberglass resin must be mixed with a catalyst (or hardener) before it will cure. You can make a mixture that is anywhere from 4:1 (four parts resin, one part catalyst) or 10:1.
The working time for a mixture of resin is different from the cure time and is somewhat short. It will begin to congeal into an unusable goo after about 5 minutes so you will need to work quickly. It will not completely cure however for another few hours.
You can extend the working time of your resin by using less catalyst and by using a wide and shallow container. Containers that are tall and narrow will cause the resin to catalyze faster because it has less surface area to vent the heat of the reaction. A 10:1 mixture will take a long time to cure and will be sticky for quite awhile. This can be good if this is your first time using fiberglass or are working on a large area.Place the fiberglass cloth and use a chip brush.

to soak the cloth with resin. You will notice the fiberglass mat go from opaque to clear as the resin catalyzes the cloth. Overlap and laminate your pieces of fiber cloth and continue working in your resin until you've covered the entire work space. Work the cloth and resin snugly around the silicone key shapes that you imbedded in your rubber mold. This will allow the silicone to register with the fiberglass jacket. Allow this to cure for 2-4 hours. Fiberglass will cure faster when using more catalyst (and in warmer temperatures).
The result should be a hard, glassy shell. Remove the clay wall and use a Dremel and cutting wheel to cut away the rough, fibrous edges. Use some sand paper to blunt the edge so you do not cut yourself while handling the finished shell (cured fiberglass is very sharp).Apply a coat of parting wax to the part of the fiberglass shell that will interlock with the surface of the other half of the finished shell. Allow it to dry for 5 minutes and then brush on (or spray) a coat of the PVA solution. You'll need to apply these both to insure that the fiberglass shells do not cure together. You only want the shells to interlock- not cure together.
Think of the parting wax and PVA as the mold release spray that you used earlier.Once this is done, follow the same steps on the othe.
Not to be confused with. Fallout Tactics: Brotherhood of Steel(digital)SeriesReleaseMarch 15, 2001Mode(s),Fallout Tactics: Brotherhood of Steel is a set in the post-apocalyptic universe. Developed by and published by, Fallout Tactics was released on 14 March 2001 for.
It sold above 300,000 units worldwide by 2008.The game follows a squad of the as it becomes engaged in a desperate war. Although the game takes place in the Fallout universe, it does not follow or continue the story of either Fallout or Fallout 2. Fallout Tactics shipped with a bonus CD when it was pre-ordered. The bonus CD included Fallout: Warfare, a table-top miniatures game based on the Fallout universe, as well as a bonus mission for the main game.
A squad uses high ground to attack deathclaws and human BeastlordsUnlike the previous two Fallout games, Fallout Tactics emphasizes tactical combat and strategy. Players have much more limited interactions with, but they can still trade with them, and some missions include dialogue. Instead of towns, Fallout Tactics centers around Brotherhood bunkers and missions.
The bunkers serve as a central point for the Brotherhood, and players can obtain the services of quartermasters, mechanics, personnel, and medics. Characters from completed missions occasionally visit the bunkers.After receiving a mission briefing from the general in charge of the bunker, the player's squad can then move to the area where the mission will take place.
Although this is usually a town, it can also be a factory, military encampment, or a Vault. There, the player is given a map of the area marked with objectives and notes.Combat in Fallout Tactics is more complicated than in the previous two Fallout games.
Unlike those, which featured an individual turn-based system, Fallout Tactics features three modes of combat: Continuous Turn-Based (CTB), Individual Turn-Based (ITB), and Squad Turn-Based (STB). In CTB, everyone can act at the same time, and action points are regenerated at a rate based on Agility. ITB is the system used in the original games. STB is a variation of that; each turn is given to a squad.
Other changes include the ability to change stance, modifiers for height, and setting sentry modes, which let characters shoot automatically in CTB upon encountering an enemy.Fallout Tactics is the first Fallout game to feature a multiplayer mode. In this mode, each player controls a squad of characters and faces off against opposing players. During game setup, players are granted a number of points with which to purchase squad members and gear.Although the main character on the single player game has to be human, recruits from the brotherhood and characters in multiplayer matches can be of any of the six races featured in the game:. Humans: Humans are the most common race on the wastelands. They do not excel in any particular area, but they do not suffer in any areas either. Humans gain perks every three levels. Super Mutants: Modified by the Forced Evolutionary Virus, super mutants are hulking beasts that are excellent at combat but lacking in intelligence and agility.
Unfortunately, they can't use small weapons such as pistols or rifles. Super Mutants gain perks every four levels. Ghouls: Ghouls are humans who have mutated due to the radiation of the wastes and have extremely long lifespans.
Although not as strong as humans, ghouls are luckier and more perceptive. They gain perks every four levels. Deathclaws: Deathclaws are massive beasts that use their bodies' size and strength to tear their enemies apart. Unfortunately, they can't use most items or wear armor and can only use melee weapons (brass knuckles, etc.), though most of their strikes will commonly knock opponents down, preventing retaliation.
Although lacking in intelligence and charisma, the bodies of deathclaws are far more durable than humans. They gain a perk every four levels. Dogs: Dogs are canines that have adapted to life in the Wastelands. Their main strengths are perception and agility, but they cannot use weapons or other tools. Dogs gain perks every two levels. Humanoid Robots: Robots are machines created to fight.

Although they always have an average amount of luck and no Charisma, Robots are strong and tough, resistant to most attacks, and immune to poison and radiation. Robots never gain perks.Plot. This article's plot summary may be. Please by removing unnecessary details and making it more concise.
( June 2015) With nuclear apocalypse looming over the world, several vaults were constructed to contain the best and brightest of humanity. By being shielded from the imminent death, the offspring of these people could reclaim and repopulate the Earth. However, before the entire network could be completed, nuclear war broke out. One of the military vaults located in California emerged from the war determined to restore civilization. Using their superior weapons, they were able to reclaim the surrounding wasteland. The members of this vault formed the Brotherhood of Steel, an organization dedicated to restoring civilization and reclaiming or developing new and better technologies.A split soon formed in the Brotherhood, however. One faction supported allowing tribals (human outsiders) to join the organization to prevent a lack of troops.
The other faction wanted to keep the Brotherhood pure and not accept outsiders. The faction against expansion won out, and the other faction was sent across the mountains on great airships to destroy the remnants of the mutant army defeated in the first. A lightning storm struck down the ships, however, and they were dispersed and forced to crash-land. One of the surviving airships crashed near the ruins of post-war. After regrouping, and free from the Brotherhood members in California who wanted nothing to do with the tribals, the crash survivors established a first base near Chicago and founded a new Brotherhood that would grow and expand by recruiting outsiders and expanding across the land.When the game starts, the Brotherhood is trying to claim territory surrounding Chicago. By offering protection to villages of tribals, the Brotherhood is able to draft recruits from among the tribals. At the beginning of the game, the player character is an Initiate, a new recruit to the Brotherhood, tasked to lead a squad of soldiers made up of available initiates.
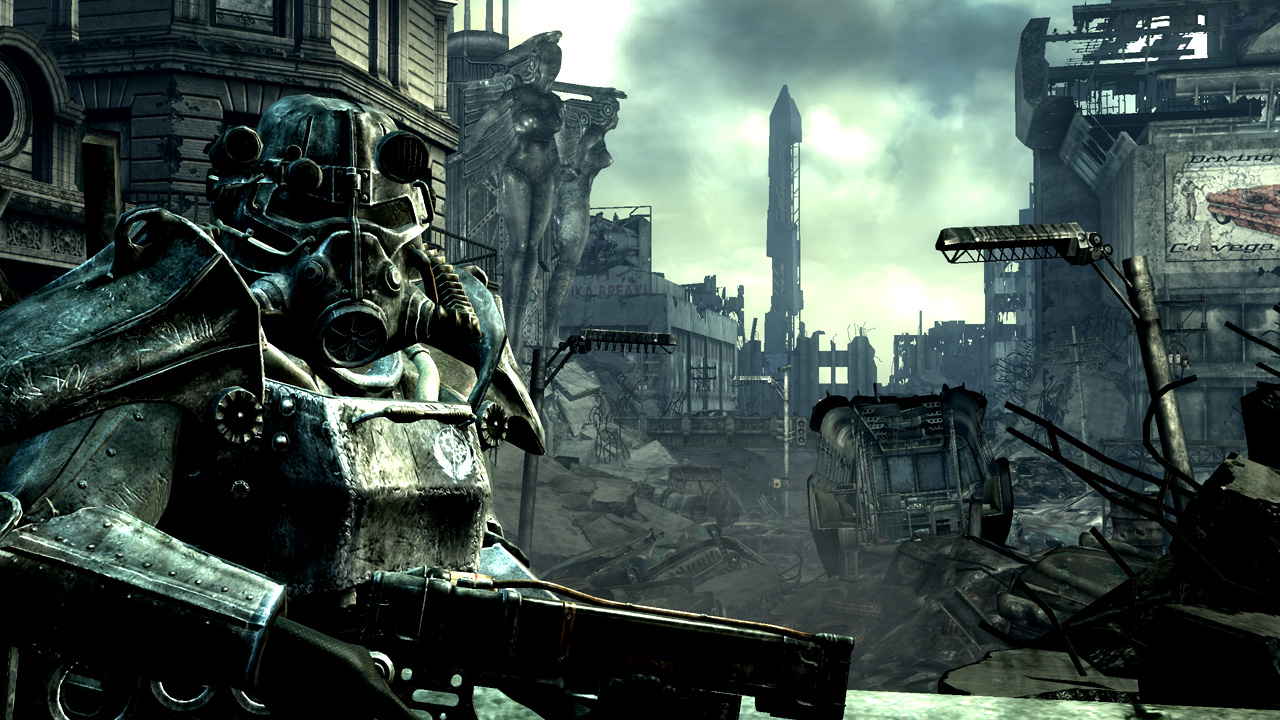
Brotherhood Of Steel Armor Fallout 76
Raiders in the area are the first challenge to the Brotherhood's authority, so the player's squad of initiates is dispatched to kill the bandit leaders and mop up the bandit threat. This section needs expansion. You can help. ( March 2019)Fallout Tactics drew from for inspiration. Fallout: Warfare Fallout: Warfare is a developed by, originally released as part of a bonus CD shipped with pre-ordered copies of Fallout Tactics. It simulates group combat and uses based upon the art of Fallout Tactics.
The game features a modified version of the. Fallout: Warfare contains five factions: The Brotherhood of Steel, Mutants, Raiders and Reavers, Beastlords, and Robots; three unit types: Grunts, Squadleaders, and Heroes; and four scenarios: Skirmish, Convoy, Treasure Hunt!, and Wild America.Reception Sales In the United States, Fallout Tactics debuted at #10 on 's computer game sales rankings for March 11–17, 2001. It rose to fourth place the following week, at an average retail price of $49, but was absent from NPD's top 10 in its third week. By 2008, the game's global sales had surpassed 300,000 copies, according to the. Reviews and awards ReceptionAggregate scoreAggregatorScore82/100Review scorePublicationScore85%Edit on wikidataFallout Tactics was well received and scored generally favorable reviews according to review aggregator. Gave it a score of 85%.
The upgraded combat system was often applauded, even if the computer AI would typically not react until shot at by the human player. The major criticisms of Fallout Tactics were its linearity compared to previous Fallout games and its emphasis on combat over open-ended. Several bugs involving vehicles in the game were never fixed. Fallout Tactics was a nominee for 's 2001 'Best Strategy Game' award, which ultimately went to. The editors wrote, ' Fallout Tactics charmed many an editor in the office, fusing the best parts of Fallout with the tactical savvy of a Jagged Alliance or an X-COM.' Canon status Due to contradictions with the story and setting of those games, the creators of considered Fallout Tactics.
With the release of Fallout 3 by, however, the existence of the game's Brotherhood splinter faction is considered at least semi-canon, with Brotherhood of Steel members in-game explaining that the Chicago-based Brotherhood featured in Fallout Tactics '.went rogue. In Fallout: New Vegas, Caesar also references having encountered a branch of the Brotherhood of Steel in Colorado.References.